作為電動汽車核心部件的動力電池目前正處于技術(shù)升級階段,主要表現(xiàn)為向更高的比能量方向發(fā)展,而新的技術(shù)變革必然面臨一系列問題。業(yè)內(nèi)許多專業(yè)人士認為,動力電池技術(shù)升級標準和安全性是首要關(guān)注。
據(jù)中國電動汽車百人會執(zhí)行副理事長歐陽明高介紹,目前,動力電池正處于變革之中,技術(shù)升級的過程中,從全球趨勢看,國際上都在向高比能量方向發(fā)展。如2018年可能大體上都在250Wh/kg,體積比能量大概在500Wh/L左右,2020年基本上在300Wh/kg,體積比能量在600Wh/L以上,到2025年大概在350Wh/kg或者是體積比能量在700Wh/L。在這個技術(shù)升級的過程中,中國還存在很多問題,如比能量提高、成本下降,但是帶來壽命尤其是安全性相關(guān)的問題,所以這一輪技術(shù)的變革會引起很多相關(guān)的問題,其實尤其關(guān)注的是標準、安全性問題。
中國電子科技集團公司第十八研究所主任肖成偉表示,目前各個國家對動力電池都做了比較全面的國家的規(guī)劃,包括日本、韓國、美國、德國等國家,設(shè)置的內(nèi)容還是從電池的產(chǎn)業(yè)鏈角度著手,如從電池的標準體系建立、關(guān)鍵的原材料、單體電池的研究、電池的產(chǎn)業(yè)化、系統(tǒng)集成應(yīng)用以及梯級利用和資源回收等。
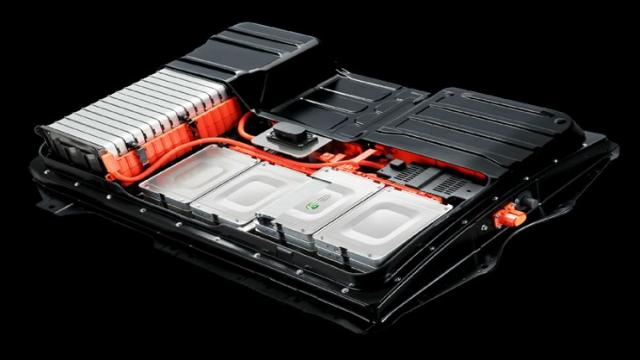
從電池到裝備、到生產(chǎn)裝備、到梯級利用,中國已形成了最為完整的產(chǎn)業(yè)鏈體系,整個產(chǎn)業(yè)投資是超過了1000億元,產(chǎn)能是超過了400億元。2015年已超過了100家電池的企業(yè)來參與動力電池產(chǎn)業(yè)化工作。但目前產(chǎn)業(yè)發(fā)展仍存在一些問題,深圳吉陽智云科技有限公司董事長陽如坤指出,如電池標準缺乏,尤其是尺寸規(guī)格標準不足;各生產(chǎn)廠家工藝不同,沒有統(tǒng)一的制造規(guī)范;動力電池制造安全性面臨嚴峻挑戰(zhàn);規(guī)模小,低端產(chǎn)能過剩,高端產(chǎn)能不足;對動力電池結(jié)構(gòu)、制造工藝研究不足;制造合格率低80~90%,安全差,成本高。同時,動力電池制造裝備也存在著制造工藝研究不足,裝備定位不清晰;裝備基礎(chǔ)差、穩(wěn)定性差、運轉(zhuǎn)率低;電池制造及裝備標準缺乏、裝備缺少依據(jù)等問題。
記者了解到,在標準化建設(shè)上,目前我國動力電池標準化已初步建立。據(jù)中國汽車技術(shù)研究中心首席專家、新能源室主任王芳介紹,2009年,電動汽車標準委員會與堿性電池標委會聯(lián)合成立了動力電池工作組,負責(zé)電池標準制定的相關(guān)工作。制定的電池標準中涵蓋電池性能、壽命、安全性、互換性、回收利用及附件6個方面的內(nèi)容。2015年5月已經(jīng)出臺了一套電池標準和測試評價,其測試的對象主要涵蓋單體、模塊和系統(tǒng),指標主要是集中于電池的一致性、電性能、壽命、安全幾個方面。
據(jù)王芳介紹,關(guān)于電性能的測試,近1~3個月以來,電池?zé)o論是國內(nèi)還是國外,主要是國內(nèi)的產(chǎn)品,送樣測試的能量密度200Wh/kg左右的樣品會比較多。目前,我國動力電池的標準化已經(jīng)初步的建立,后期的測試以及標準化的工作需要根據(jù)動力電池的研發(fā)、推廣和應(yīng)用不斷的細化、補充和完善,也會根據(jù)新的問題出現(xiàn)不斷改進。
企業(yè)標準也在不斷完善。據(jù)了解,目前比亞迪已經(jīng)做到電池模組標準化,在整車的使用上可以進行擴展。另外,比亞迪從2012年開始關(guān)注電池回收。比亞迪股份有限公司電池技術(shù)部經(jīng)理江文峰表示,由于電池回收利潤較高,目前沒有統(tǒng)一的回收標準,行業(yè)急需一個公正合理的電池判定標準。陽如坤建議,在制定電池標準時,規(guī)格按照尺寸作為主參數(shù),而不是把容量作為主參數(shù),這樣真正才能體現(xiàn)電池的規(guī)格。而電池的安全性主要有三個方面,設(shè)計、制造、使用。同時他還建議制定動力電池制造的路線圖,立項研究電池的工藝、制造方法和制造裝備;從裝備的發(fā)展來統(tǒng)一規(guī)劃,專門來立項;要建立動力電池制造標準和制造裝備的標準。 |